Perth Distribution Centres: Efficiency with One Stop Pallet Racking
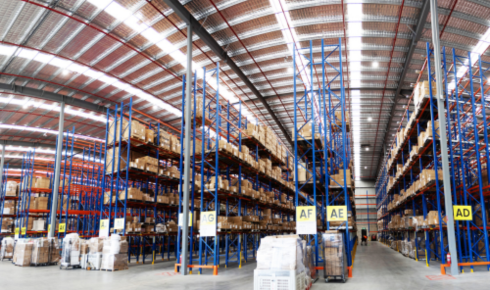
Discover how Perth distribution centres are enhancing their operational efficiency with innovative one-stop pallet racking solutions. This article delves into the benefits of utilizing advanced storage systems to streamline warehouse operations, improve inventory management, and maximize space utilization in the bustling logistics hub of Perth, Australia.
One Stop Pallet Racking plays a pivotal role in revolutionizing storage solutions, offering Perth distribution centers enhanced efficiency. These systems not only optimize space but also simplify inventory management, leading to seamless operations. By embracing these innovative solutions, warehouses in Perth boost their logistical capabilities in a competitive environment.
Importance of Efficient Distribution Centres
Efficient distribution centers play a crucial role in the supply chain management of businesses. These centers are responsible for receiving, storing, and shipping goods to various destinations, ensuring that products reach customers in a timely manner. By optimizing their operations, distribution centers can reduce lead times, minimize inventory holding costs, and improve overall customer satisfaction. Efficient distribution centers also help businesses meet the demands of a dynamic market by enabling quick response to changes in customer preferences, production schedules, and external factors such as weather disruptions or supplier delays.
Furthermore, efficient distribution centers contribute to cost savings and increased profitability for businesses. By streamlining processes, reducing waste, and enhancing inventory management, distribution centers can lower operational expenses and improve the utilization of resources. This not only benefits the bottom line but also enhances the competitiveness of the business in the market. Moreover, efficient distribution centers can support sustainability initiatives by minimizing carbon emissions through optimized transportation routes, reducing packaging waste, and implementing energy-efficient practices. In essence, efficient distribution centers are the backbone of a well-functioning supply chain, enabling businesses to meet customer demands efficiently while driving profitability and sustainability.
Advantages of One Stop Pallet Racking Systems
One of the key advantages of one-stop pallet racking systems is the convenience they offer in streamlining the storage and organization of goods in warehouses and other industrial settings. By providing a comprehensive solution that includes all the necessary components such as upright frames, beams, wire decking, and accessories in one package, these systems simplify the procurement process for businesses. This not only saves time and effort in sourcing individual components from different suppliers but also ensures compatibility and seamless integration of all parts for efficient use. Additionally, having a single supplier for the entire pallet racking system can lead to cost savings through bulk purchasing discounts and reduced shipping expenses.
Another significant advantage of one-stop pallet racking systems is the scalability and flexibility they provide to accommodate changing storage needs and space constraints. These systems are designed to be easily adjustable and reconfigurable, allowing businesses to adapt to evolving storage requirements without the need for extensive downtime or costly renovations. Whether a business needs to expand its storage capacity, reorganize its inventory, or optimize its warehouse layout, a one-stop pallet racking system offers the versatility to make these adjustments quickly and efficiently. This flexibility not only enhances operational efficiency but also maximizes the utilization of available space, ultimately improving the overall productivity and profitability of the business.
One Stop Pallet Racking Accessories provide additional versatility to storage systems by offering a range of components that enhance organization and efficiency. Available at One Stop Pallet Racking Accessories, these additions allow businesses to tailor their storage solutions to specific needs, further improving space utilization and operational effectiveness.
Design Considerations for Perth Distribution Centres
Design considerations for Perth distribution centers must take into account the unique geographic and environmental factors of the region. Perth’s hot and dry climate requires efficient cooling and ventilation systems to ensure optimal working conditions for employees and to protect perishable goods. Incorporating sustainable design elements such as solar panels and rainwater harvesting systems can help reduce energy costs and minimize the environmental impact of the distribution center. Additionally, Perth’s susceptibility to bushfires means that fire safety measures, such as adequate fire protection systems and fire-resistant building materials, must be prioritized in the design process.
Furthermore, the strategic location of Perth as a major transportation hub in Western Australia necessitates careful planning of access points and traffic flow within the distribution center. Designing efficient truck loading and unloading bays, as well as optimizing internal circulation routes for forklifts and other equipment, can help streamline operations and minimize congestion. Considering the proximity of major highways and ports, incorporating dedicated areas for container storage and handling can enhance the distribution center’s logistical capabilities and facilitate seamless transportation of goods to and from the facility. Overall, a well-thought-out design that integrates both operational efficiency and sustainability features is essential for the successful functioning of distribution centers in Perth.
Maximizing Storage Space with Pallet Racking
Maximizing storage space with pallet racking is essential for warehouses and distribution centers looking to efficiently store large quantities of goods. Pallet racking systems are designed to maximize vertical space utilization, allowing businesses to store goods in a compact and organized manner. By utilizing the height of the warehouse, pallet racking systems help businesses make the most of their available storage space. With various types of pallet racking systems available, such as selective, drive-in, and push-back racking, businesses can choose the system that best suits their inventory requirements and space constraints. Selective pallet racking, for example, is ideal for fast-moving goods that require easy access, while drive-in racking is suitable for high-density storage of homogeneous products.
Furthermore, maximizing storage space with pallet racking can also lead to improved inventory management and operational efficiency. By organizing inventory vertically, businesses can easily locate and access goods, reducing picking and retrieval times. This results in enhanced productivity and smoother warehouse operations. Additionally, efficient use of storage space means that businesses can store more inventory on-site, reducing the need for off-site storage facilities and streamlining supply chain operations. Overall, maximizing storage space with pallet racking not only optimizes storage capacity but also contributes to cost savings and improved workflow within the warehouse environment.
Automation and Technology in Distribution Centre Operations
Automation and technology play a crucial role in modern distribution center operations, revolutionizing the way goods are received, stored, picked, packed, and shipped. Automated systems such as conveyors, sorters, robotics, and automated guided vehicles (AGVs) streamline the movement of goods within the distribution center, increasing efficiency and reducing manual labor. These technologies enable faster order fulfillment, improved accuracy, and enhanced productivity, ultimately leading to cost savings and better customer satisfaction. Advanced warehouse management systems (WMS) and inventory management software further optimize operations by providing real-time visibility into inventory levels, order statuses, and performance metrics, allowing for better decision-making and resource allocation.
In addition to internal operations, automation and technology also enhance the connectivity and collaboration between distribution centers, suppliers, and customers. Cloud-based platforms, IoT devices, and data analytics tools enable real-time communication, monitoring, and information sharing across the supply chain network. This seamless flow of data improves inventory forecasting, demand planning, and replenishment strategies, leading to reduced stockouts, lower carrying costs, and improved inventory turnover. Furthermore, technologies like RFID, barcode scanning, and autonomous drones enhance traceability and security, ensuring accurate tracking of goods and minimizing the risk of errors or theft in distribution center operations.
Safety Measures in Pallet Racking Systems
Safety measures in pallet racking systems are crucial to prevent accidents and ensure the well-being of warehouse workers. One of the primary safety measures is regular inspection and maintenance of the pallet racking system. Inspections should be conducted by trained personnel to check for any signs of damage, such as bent beams, missing or damaged safety pins, or overloading. Any issues should be addressed promptly to prevent structural failures that could lead to collapse. Additionally, it is essential to ensure that the racking system is properly installed according to manufacturer guidelines and local regulations. Proper installation includes securing the racks to the floor, using appropriate weight capacities, and ensuring proper spacing between racks to prevent accidents.
Another important safety measure in pallet racking systems is training employees on safe practices for working with the system. Workers should be educated on how to load and unload pallets correctly, avoid overloading shelves, and use appropriate equipment such as forklifts or pallet jacks. Safety training should also include procedures for reporting any safety concerns or incidents promptly. Additionally, clear signage and labeling should be used to indicate weight capacities, aisle directions, and emergency procedures. By implementing these safety measures and providing ongoing training, companies can create a safer work environment and reduce the risk of accidents in pallet racking systems.
Case Studies of Successful Perth Distribution Centres
Perth boasts several successful distribution centres that serve as shining examples of efficient logistics management. One such case study is the Perth Airport Distribution Centre, strategically located to capitalize on the city’s transportation infrastructure. This state-of-the-art facility leverages advanced technology and automation to streamline operations, offering seamless movement of goods in and out of the centre. By optimizing storage space and implementing sophisticated inventory management systems, the Perth Airport Distribution Centre is able to cater to the diverse needs of its clients while maintaining cost-effectiveness and timely deliveries. Its success lies in its ability to adapt to changing market demands, ensuring that it remains a key player in the competitive distribution industry in Perth.
Another notable case study is the Malaga Distribution Centre, which has established itself as a key player in the logistics landscape of Perth. This centre stands out for its commitment to sustainability and eco-friendly practices, setting a benchmark for environmentally responsible distribution operations. By incorporating green technologies and energy-efficient practices into its daily operations, the Malaga Distribution Centre not only reduces its carbon footprint but also sets a positive example for the industry. Its success can be attributed to its focus on innovation and continuous improvement, constantly seeking new ways to enhance efficiency and reduce waste. The Malaga Distribution Centre serves as a model for other distribution centres in Perth looking to achieve operational excellence while minimizing their environmental impact.
Sustainable Practices in Distribution Centre Management
Sustainable practices in distribution center management are essential for reducing environmental impact and operating costs while meeting consumer demand. One key aspect of sustainable practices is optimizing transportation and logistics to minimize fuel consumption and carbon emissions. This can be achieved through route optimization, efficient loading and unloading processes, and choosing eco-friendly modes of transportation such as electric vehicles or trains. By reducing the carbon footprint of transportation, distribution centers can contribute to a healthier environment and lower operational costs.
Another important sustainable practice in distribution center management is waste reduction and recycling. Distribution centers generate a significant amount of waste from packaging materials, damaged products, and outdated inventory. Implementing recycling programs, reducing packaging waste through sustainable packaging solutions, and donating excess inventory to charitable organizations can help minimize waste and support a circular economy. By adopting sustainable practices in waste management, distribution centers can reduce landfill waste, lower disposal costs, and demonstrate their commitment to environmental stewardship. Overall, sustainable practices in distribution center management are crucial for achieving long-term profitability and environmental sustainability.
Future Trends in Distribution Centre Efficiency
The future trends in distribution center efficiency are poised to revolutionize the way goods are managed, stored, and distributed. One key trend is the integration of advanced technology such as automation, robotics, and artificial intelligence (AI) into distribution center operations. Automation technologies like autonomous mobile robots are becoming increasingly popular for tasks such as picking and packing, leading to faster and more accurate order fulfillment. AI-powered predictive analytics are also being leveraged to optimize inventory management, demand forecasting, and routing, reducing costs and improving overall efficiency. With the advancement of technology, distribution centers are expected to become more agile and responsive to customer demands, enabling faster delivery times and improved customer satisfaction.
Another future trend in distribution center efficiency is the emphasis on sustainability and environmental stewardship. As the world grapples with climate change and environmental degradation, distribution centers are under increasing pressure to reduce their carbon footprint and adopt eco-friendly practices. Companies are exploring innovative solutions such as green buildings, energy-efficient equipment, and renewable energy sources to minimize their impact on the environment. Additionally, there is a growing focus on implementing circular economy principles in distribution center operations, such as reusing and recycling materials, extending product lifecycles, and reducing waste. By embracing sustainability practices, distribution centers can not only reduce costs and improve operational efficiency but also contribute to a more sustainable future for the planet.
Choosing the Right Pallet Racking System for Your Perth Centre
When selecting the ideal pallet racking system for your Perth center, it is crucial to consider the specific needs and requirements of your operation. Firstly, assess the available space in your warehouse to determine the most suitable racking system that maximizes storage capacity while ensuring efficient utilization of the floor area. For example, if you have a high ceiling, a selective pallet racking system might be ideal for easy accessibility and picking of goods. Conversely, if you have limited floor space but high vertical space, a narrow aisle racking system could be more suitable to optimize storage density.
Secondly, factor in the nature of your inventory and handling equipment to choose a pallet racking system that aligns with your operational workflow. If your inventory consists of perishable goods or items with expiration dates, a FIFO (First In, First Out) system like drive-in racking may be preferred to ensure proper stock rotation. On the other hand, if you deal with a wide variety of products with varying turnover rates, a dynamic storage system such as push back racking could offer flexibility and efficiency in managing inventory. By carefully evaluating these aspects, you can select the right pallet racking system that enhances the productivity and functionality of your Perth center.